Bizav Training & Services, Inc.
Mr. James Deuvall July 12, 2010 President CAVU Companies 103 Burrows Road West Winfield, NY 13491
RE: CC of letter sent to FAA
As an instructor and check airman of turbojet aircraft for over 26 years, I have trained a multitude of pilots on the subject of performance. I have catalogued numerous methods and observed several commercially available products that pilots have presented to me during class. The inappropriate methods range from not performing the calculations at all, to elaborate, but incorrect, rules of thumb. The products I have tested range from downright incorrect and deceptive, to thorough, clear and comprehensive. Like you, I am on the forefront of promoting aviation safety and I hope you will find this letter informative. First, I would like to mention a publication that is an excellent primer on the issues I will be discussing. The book, which can be found on Amazon.com, is called Aircraft Performance-Myths and Methods by James Deuvall. I recommend this book to all my students and even the highest time pilots find it very helpful. The proper use of Part 25 performance charts, irrespective of the manufacturer or model, is a complex process. The obstacle clearance method discussed in most, if not all, part 142 schools, while consistent with the AFM, are wholly inadequate to the preparation of pilots flying in todays changing environment. The reason for this is that all AFMs use, as an obstacle clearance example, the rare and simplistic condition of clearing a single, relatively short, known obstacle. This example calculation is very straightforward and even somewhat intuitive. Rarely is any time spent instructing pilots how to meet a climb gradient, such as a departure procedure (DP), ODP or SID. Because of this, most pilots, as well as some vendors, use that same intuitive methodology to meet extended climbs associated with DPs. As a result, erroneous maximum weight calculations are the rule rather than the exception. If an operator is not using a performance calculator, I can assure you that either the charts are not being referred to at all or are incorrectly done so. It only takes a matter of a few minutes to uncover the potentially life-threatening errors manual methods produce. Now, I have also found that the use of a calculator, by itself, does not provide adequate assurance of correct computations either. It is very important to understand that calculators also use a methodology and I have found that some popular calculators simply automate the same improper methods that pilots use manually. The best known of these is UltraNav. I have encountered this product numerous, numerous times as an instructor. UltraNav self-proclaims and promotes, as a benefit of their product, several erroneous assumptions. Every Part 25 aircraft, by certification, uses a specific profile to construct the AFM data. That profile, referred to as the Net Takeoff Flight Path, is absolutely integral to the validity of the numbers published in the AFM and mentioned in both Part 121, 125 and Part 135 regulations. In order for the aircraft to achieve the values in the AFM, the aircraft must fly the profile precisely. If a calculation deviates from this profile, none of the promised performance, within the AFM, can be assured. The profile requires ALL aircraft to climb, within second segment, to a maximum altitude and no higher. There are a few exceptions however, for example manufacturers who have provided specialized charts for extended climbs while maintaining engine time limits, but most aircraft have mandatory level-offs from 400 to 1500 feet. This is one of those non-intuitive computations typically overlooked by pilots attempting to compute performance by hand and almost universally not observed during Part 142 simulator sessions. The intuitive, but incorrect, method would be to not lower the nose if an engine failure occurs and hold V2 no matter what altitude is required to clear obstacles. This is exactly what most simulator instructors teach and what the UltraNav performance calculator calculates. Unfortunately, as I mentioned previously, the resulting flight path of holding second segment beyond the limits of the AFM is entirely hypothetical. UltraNav calls this always-in-second-segment flight path True Flight Path, which they have coined within their product. The validity of this path is entirely false. Abacus and AFMsolutions (written by the same gentleman who wrote UltraNav) also make similar assumptions. The only performance calculator that follows the Net Takeoff Flight Path and incorporates the engine-time and other system limits correctly is the CAVU Companies product EFB-Pro. The Cessna CPCalc product, while certified under the same provisions as an AFM, does not appear to follow its own print version of the AFM Net Takeoff Flight Path procedure. If you enter a climb gradient in CPCalc, lets say a 6% climb to some altitude above 2500ft; the calculator will provide the total distance from the end of the runway to the beginning of the level-off segment. If you divide that value into the AFMs maximum level off altitude, you will get a gradient that is less than the 6%. This can only occur if the path of the aircraft falls below the 6% gradient during the climb or the level-off (third segment) has been initiated above the maximum level-off height. This is an apparent disconnect between the AFM and the calculator. The other non-manual method, which is becoming increasing more popular, is the use of runway analysis. There are several vendors of such products available to business class jet operators, but the most popular, I believe, is APG (offered free through ARINC Direct, a factor in its popularity). While I have nothing against the actual calculations provided, I have observed consistent misuse of this tool. Runway analysis comes to us from the airline industry. Within that environment, runway analysis is a safe and well-managed practice. Airlines typically use an internal engineering department to construct escape procedures and flight test those procedures with average ability crew and standardized equipment in mind. Line pilots are then familiarized, during simulator sessions, with the procedures they will encounter along their scheduled routes. Runway analysis, when utilized within the part 135 and 91 worlds, poses many unique safety issues. Unlike the airlines, who train to proficiency on a handful of escape procedures, the Part 135 crew potentially faces several thousand uniquely modified DPs at a moments notice. I have never encountered an operator who was required to provide, nor has voluntarily provided, enhanced simulator/flight training specific to runway analysis even when authorization was needed to use this method. During training, what I invariably encounter are crews who refer to the maximum weight listed for a runway and then the entire process ends there. Operators are universally unaware of the special procedures involved in using runway analysis correctly and safely. Here are just a few that I have encountered. Since the modified procedure will most likely deviate from the normal departure procedure, crews must set up FMSs and brief differently. Rarely, if ever, is this done. Crews are universally unaware of the reduced safety margins, both laterally and vertically, utilized in constructing the unique runway analysis DPs (AC120-91). I have never seen an operator actually flight test the procedure, as the airlines do. Briefing points should include items such as when the DP procedure becomes obsolete (The point where the modified DP deviates from the normal procedure. When the aircraft passes this point, the aircraft is committed to the normal procedure). Since the FMSs maybe set up independently, one for the SID, the other for the modified DP, a thorough understanding of who will be the pilot flying (PF) must be briefed in the event of an engine failure. Routinely the modified DP will incorporate a hold, the location and entry of which must be briefed. Additionally, the method of navigating must be considered since wind drift may lead to a flight path that lies outside of the safety area. As inspectors and examiners, I am aware that you can not advocate the use of specific products as I am at liberty to do; however, I would encourage you to contact me and/or acquire a copy of the aforementioned book to learn more about this area of flight safety that has gone largely unnoticed by the industry. I should also mention that in no way do I financially benefit from any of the products mentioned. I am sharing this information with you as a professional pilot and instructor devoted to the continuing safety of general aviation. With regards,
Darrell Rahn
(Reprinted from NBAA Airmail )
You offer a good opportunity to bring a different, and I think more important, perspective to this. The "battle" between APG and EFB-Pro (that seems to be the two camps these days) is not which one has the most features. Though none come to mind at the moment, I'm sure CAVU has its fixes to make too. My goodness, I have a $500K avionics suite that keeps needing "upgrades".
Mr. Gordon hits it on the head with his last question, but he's only hinting (perhaps out of politeness) at the real issue.
This is a difficult subject to approach since any comment I make may (and probably will be) be construed as bashing APG. So let me say up front, I don't care which system you use; I only refer to them by name because everyone seems to understand what I am referring to when I do. I'm really referring to the whole runway analysis approach. I have found, even in my own department, that there is an underlying difference in, what I call, a "perception of importance to safety" between pilots/operators who support APG's approach versus those who do not. The difference fills the spectrum from those who run the numbers only to justify filling the airplane up to max gross to acknowledging that there is a safer way but "we get it free with ARINC and besides our POI has approved us to use it". Across the board there seems to be a sort of level-1 thinking only, ie "APG says we can go out with this weight, thats it, end of discussion" when in fact there are several very important, even life-threatening, issues dealing with the actual logistics of implementing the use of special DPs.
First, it should go without saying, you don't get anything for nothing. If you go out heavier at any airport OEI, physics dictate that you will be lower to the ground. APG is not a magic wand. Your obstacle clearance will be less and your left and right obstacle clearances will be less (way less) than the normal departure.
Second, you mention Rodger Hemphill and his wealth of knowledge. I'm sure that is true, but no one that I've talked to there was one. There's a big heap between an engineering a departure and actually sitting in the front seat, on a rainy day, mountainous terrain and an engine fails. Even in the sim, it can get your heart pumping.
Third, there is a big difference between 121 and 135/91 operations. I seem to get the most push back from guys who come from the airlines who believe this is the way it should be done. But wait, I've flown for the airlines. Every 6 mths I was back in the sim training on the "escape procedures" I would encounter on my route and at most there were like two. In fact, the crew had to be checked off to use them. Plus the company had flight tested all the procedures with our own equipment. That kind of validation is not done by any operator that I know of. I've never heard anyone come up with a good solution to the training proficiency issue. We barely have time to cover one special DP in the sim and most of the time the instructor is not familiar with the special DP and basically just positions us at the end of the runway.
Fourth, all the special DPs had to be manually entered in a second FMS. The FMS I use has event driven switch-overs and still it takes 4-5 seconds while my side side refreshes with the routing from the other side. 4-5 seconds may not seem like a long time, but it seems like an eternity when things are hitting the fan and happening fast without any nav reference. Referring to the post on over automation, it seems that automation always seem to fail at the worse time.
Fifth, briefings. With 30 pilots in our department, I can say the standardization of briefings of dual departures with an immediate hold is a pipe dream. Here's an example, on the APG print out, a level height is sometimes given to you. The problem is its a "fixed" MSL value. So crew would brief this altitude to level-off. Do you remember "high to low, look out below"? When you are dealing with altitudes in the 400-1500 ft range, these things matter. One reason we went with EFB-Pro is that their level-off altitude is corrected for temperature and pressure differences from ISA. We can actually brief that number, but I digress.
There are many more issues and stories but let me end with this. Several years ago, we came out of Vegas in a global. The boss wanted to go non-stop London. Problem was he wanted to leave at four in the afternoon in the middle of the summer. I ran the numbers using EFB-Pro and my co-captain looked up APG numbers. To make a long story short, I determined we had to make a stop or go when it was cooler. The owner, who wanted to go when he wanted to go had been told by his "friends" that they do it all the time in their globals, and my co-captain!!! both argued with me. I prevailed and departed without incident on the 14000ft runway. After leveling off, the owner stuck his head in the door and said essentally, "Thank you for sticking to your guns. Even sitting in the back, I could tell how long it was taking to get airborne, in fact I was getting a little nervous about it and that with both engines running. I spent $40M on this airplane and its an eye opener to see how marginal the performance is." Again, a "perception of importance to safety". In the final anaylsis, what are we really relying upon for our safety. Unfortuately, for a number of us, it appears to be the reliability of the engines.
I'm sure this will tip off a firestorm of comments, becasue people are passionate about what they have, but I have come to the conclusion that using runway analysis, practically speaking, only has a very limited use in 135/91 operations and even then only with specific proficency training and SOPs in place.
Jeff M
Standards Captain
|
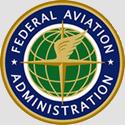
Coby Johnson, Manager March 3, 2007 Flight Operations Branch, AFS-410 Federal Aviation Administration 800 Independence Ave., S. W Washington, DC 20591
Dear Dr. Deuvall
In response to your presentation dealing with preflight takeoff calculations, runway analysis and obstacle clearance, I would like to take this opportunity to thank you for taking the initiative to shed more light on an area of aircraft performance that has accumulated a great deal of confusion over the years.
While the FAA can not endorse a specific product, I can speak to the FAAs position regarding the authority of the aircraft flight manual (AFM) in conducting preflight planning calculations.
First, allow me to dispel the notion that the AFM contains takeoff procedures that have been included for certification purposes only and have no operational relevance, particularly preflight planning.
The profiles described within the AFM are considered by the FAA to be the only acceptable procedures.
Second, if the AFM describes a takeoff path profile, including level-off or transition periods, engine time or other limits, those criteria must be considered when calculating appropriate engine inoperative obstacle clearance performance planning and weight restrictions. This is particularly true for obstacles or gradients that extend above 1500 feet.
Third, the use of rules of thumb, work-a-rounds or other methodologies not specifically described within the AFM or subsequently authorized by the manufacturer are not approved by the FAA. This would include, but is not limited to, extrapolating performance values beyond the limits of a chart or substituting an enroute altitude for the airport elevation when entering a second segment chart.
While none of these clarifications diminish the pilots authority to deviate from any regulation to meet an in-flight emergency, the intent of this position is to improve the safety margin of all operations operated under commercial or general regulations.
Again, whether you are presenting to Part 91, 135, 91k or 121 operators, please extend my appreciation for their continued efforts to improve their skills and knowledge as professional pilots.
Thank you
Coby Johnson Manager, AFS-410
|