Commercial operators are required to clear obstacles by 35 feet while on a Net Takeoff Flight Path. This can be accomplished two ways:
1) A path can be constructed that differs from the DP that meets narrower and lower to the ground safety margins and all the obstacles can be identified along that path until it terminates in a holding pattern. This requires the pilots to manually set up the second FMS with this new route (they are not stored). See the letter below from a previous user of this method and also the letter from the check airman. This method only theoretically protects you if the engine fails while on the runway.
2) The published departure procedure was constructed to provide obstacle clearance. While the gradient displayed may include non-obstacle barriers (ie ATC limitations, noise abatement) there is an Obstacle Clearance Surface beneath the SID that represents the obstacles and terrain. EFB-Pro uses this OCS surface, plus the added regulatory obstacle clearance margin, to create the Net gradient, above which the aircraft's Net Takeoff Flight Path will stay. In other words, you will always fly the DP path regardless of whether you lose an engine or not. This method provides protection regardless of when the engine fails without requiring a hold.
What does the FAA say ?
|
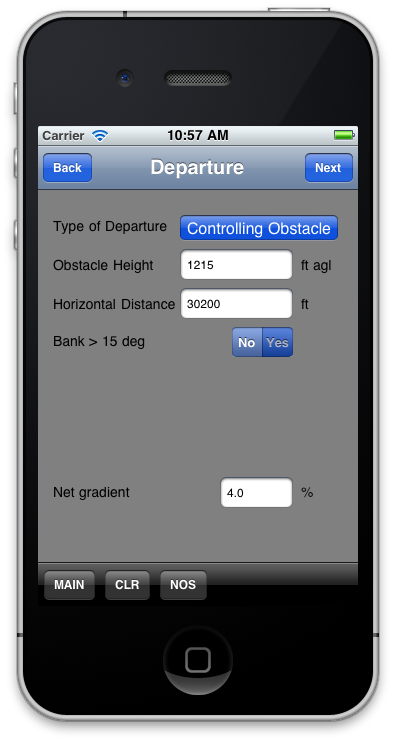
When a departure procedure is not charted or described, the pilot must manually calculate the gradient from the height of the obstacle in the flight path and the distance from the runway. This value must also be modified to reflect the reference height as prescribed by the manufacturer and the clearance height as dictated by regulation. The resulting gradient is then net and must be further modified to reflect aircraft certification, number of engines and operating regulations to render a gradient. This calculation is performed automatically and transferred to the weather page as the target required gradient.
|
"I've been flying these aircraft for over 30 years. When this department first started, we used APG. Even when we knew that we would get a V1 cut, we would brief to the point of deciding who would press what buttons and switches, the holding pattern entry, everything. We have event driven FMS so I only had to press a button to switch over the FMS.
When we actually practiced it in the sim, as busy as it got, it wasn't unusual for us to still mix it up. It was very apparent that this was un-doable on a regular basis on the line. Perhaps airlines that can train crew to a specific route schedule and a handful of special procedures, but its totally impractical for part 91 and 135 operators who never know what airport they will be departing from. Having to keep track of when the special procedures depart from the SID further complicates the problem. I can't over emphasize how distracting and busy it gets, even in the sim, during an engine out scenario. Keeping track of the new routing with IMC conditions and knowing that terrain is out there is just not practical.
Crews that use APG are kind of kidding themselves or maybe intentionally trying to placate regulatory requirements that this is a safe mechanism for assuring obstacle clearance. Most crews I know that use APG don't train in the sim for the product and really have no idea what they are buying into. And remember, none of these procedures have been flight tested."
Steve B, Chief Pilot
Important Letter from Instructor/Check Airman
|